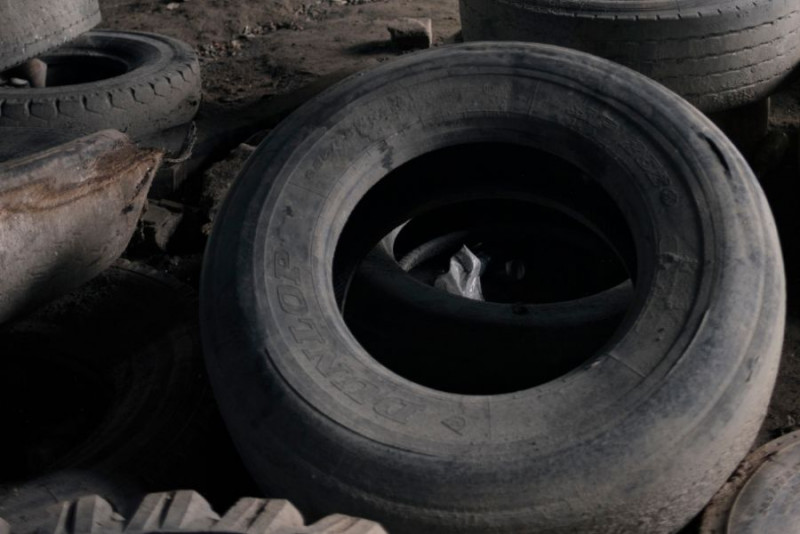
Co roku na polski rynek trafia od 280 tys. do 350 tys. ton zużytych opon. Tymczasem krajowe zakłady recyklingu mogłyby zagospodarować nawet 400 tys. ton rocznie. Znaczna część tych odpadów znika z systemu, trafiając na dzikie wysypiska lub do spalania, co budzi sprzeciw recyklerów. Ze zużytych opon można odzyskać takie produkty, jak sadza techniczna, olej popirolityczny czy stal, które mogą zastąpić surowce pierwotne przy produkcji nowych.
Jak wynika z raportu Polskiego Stowarzyszenia Recyklerów Opon „Historia, która kołem się toczy”, Polska zajmuje niechlubne pierwsze miejsce w Unii Europejskiej pod względem liczby niezagospodarowanych opon, a także ma ma najniższy efektywny poziom recyklingu i odzysku. W 2019 r. rzeczywisty odzysk wyniósł 79%, a w 2021 r. – 74,7%. Poziom recyklingu był jeszcze niższy, wynosząc odpowiednio 47% i 44,5%. To niepokojące dane, zwłaszcza że podmioty wprowadzające opony na rynek są zobowiązane ustawowo do odzysku minimum 75% tonażu opon z poprzedniego roku, z czego 15% musi być poddane recyklingowi materiałowemu. PSRO postuluje zwiększenie tych limitów, podkreślając brak ekonomicznego i technicznego uzasadnienia dla ich obecnego poziomu.
Krzysztof Wróblewski, prezes zarządu Contec, zwraca uwagę, że choć przetwarzanie opon w Europie jest trendem, to w Polsce nadal duża część zużytych opon trafia do cementowni jako opał. – Trochę się na to nie godzimy, natomiast widzimy największy nacisk ze strony producentów opon. To oni potrzebują surowców zrównoważonych do tego, żeby spełnić swoje cele ESG. To oni nas wspierają w tym, żebyśmy tak projektowali nasze produkty, żeby oni mogli ich użyć – wskazuje ekspert. Podkreśla również, że choć przetwarzana cyrkularnie jest dużo mniejsza część opon, niż jest to możliwe, to firmy inwestują w nowe zakłady i wspierają innych graczy. – W Europie sytuacja nie wygląda jakoś spektakularnie lepiej, bo te technologie, zwłaszcza recyklingu chemicznego, są jeszcze stosunkowo młode, nie osiągnęły masy krytycznej. Natomiast cieszę się, że konkurenci też budują duże zakłady, bo będzie nam trochę łatwiej edukować cały rynek, który jest dla nas praktycznie nieograniczony, żeby przerzucić się na gospodarkę obiegu zamkniętego – tłumaczy Krzysztof Wróblewski.
W Polsce rośnie udział odzysku materiałowego, który polega na rozdrabnianiu opon na mniejsze kawałki w celu odzyskania stali, tekstyliów i granulatu gumowego. Oczyszczona i przetopiona stal znajduje szerokie zastosowanie, tekstylia mogą być używane do produkcji betonu zwiększając jego odporność na pękanie, a granulat gumowy jest z powodzeniem wykorzystywany m.in. w budownictwie drogowym, poprawiając wytrzymałość nawierzchni asfaltowych i przyczepność. Firma Contec idzie o krok dalej, stosując autorską technologię pirolizy Molten. Do rozgrzania reaktora, w którym zachodzi proces pirolizy, wykorzystuje się mieszaninę ciekłych soli, co również wspiera ideę obiegu zamkniętego. Jest to beztlenowe spalanie w kontrolowanych warunkach, które pozwala na wytworzenie z zużytych opon oleju popirolitycznego i odzyskanej sadzy technicznej. Te surowce mogą być wykorzystywane w wielu branżach, ale ich kluczowe zastosowanie to produkcja nowych opon – przemysł oponiarski odpowiada za 70% wykorzystania sadzy technicznej.
– Jak przyjeżdża do nas opona, to 85% z niej zamienia się na surowce, które trafiają z powrotem do opon. Te trzy główne strumienie surowców to stal, odzyskana sadza techniczna, czyli czarny pigment, proszek, który służy do wzmacniania gumy i plastików, oraz olej popirolityczny, który można używać jako surowiec na rynku chemicznym – wyjaśnia prezes Krzysztof Wróblewski. Pozostałe 15% masy opony jest przetwarzane na energię, co pozwala firmie na samowystarczalność energetyczną, korzystając wyłącznie z zielonej elektryczności.
– Trudno o lepszy przykład gospodarki obiegu zamkniętego, jak z trudnego produktu do zagospodarowania, na który jeszcze niedawno jedyny pomysł, jaki mieliśmy, to go spalić, odzyskujemy surowce, które trafiają do produkcji nowych opon – podsumowuje Krzysztof Wróblewski.
fot. freepik.com
oprac. /kp/